Introduction to white cement
White or grey cement is used to make various colored cement. As a foundation, Portland cement is utilized. The use of white cement as a foundation is expensive. Only red or brown cement may be created when grey cement is used. Colored cement is made from Portland cement mixed with 5-10% pigment. Because the pigment cannot be evenly dispersed throughout the cement by mixing, the cement and pigment are usually ground together.
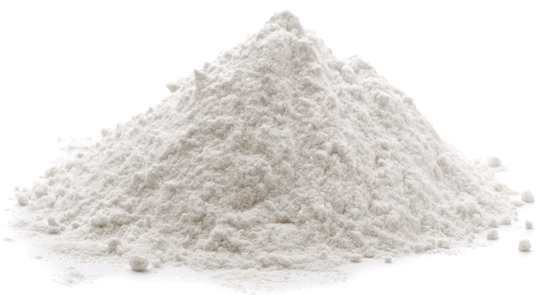
white cement
Color stability under exposure to light and weather, a fine state of division, a chemical composition that is neither influenced by nor deleterious to the cement, and the lack of soluble salts are all qualities needed of a pigment for colored cement. It is also called White Portland Cement/ White Ordinary Portland Cement.
The manufacturing method for white Portland cement is virtually identical to that of OPC. Due to the scarcity of raw resources, particularly the type of limestone necessary for making white cement, two well-known brands of white cement, Birla White and J.K. White Cements, are made near Jodhpur.
Limestone with high purity is utilized as a raw material (96 percent CaCo3 and less than 0.07 percent iron oxide). China clay with an iron concentration of 0.72 to 0.8 percent, silica sand, fluorspar as flux, and selenite as a retarder are the additional raw ingredients. Refined furnace oil (RFO) or gas are utilized as fuels.
Seashells and coral can also be utilized as raw materials for white cement manufacturing. White cement has virtually identical characteristics to OPC. White cement is often powdered finer than grey cement. The whiteness of white cement, as determined by the ISI scale, must be at least 70%. The Hunters Scale may also be used to determine whiteness. According to the Hunters scale, the value is usually around 90%.
Table: Chemical requirements for White Portland cement
Sl. No. | Characteristic | Requirement |
1 | By using the formula, the ratio of “percentage of lime” to “percentage of Silica, alumina, and iron oxide” is determined.
|
1.02<Ratio>0.66 |
2 | Iron oxide, % by mass | <1% |
3 | Insoluble residue, % by mass | <2% |
4 | Magnesia, % by mass | <6% |
5 | Total Sulphur content calculated as so3, % by mass | <2.75
<3 when C3A |
Note: The tricalcium aluminate content is calculated as follows:
C3A = 2.65 (Al2O3 % by mass of cement excluding any insoluble residue)-1.69 (Fe2O3 % by mass of cement excluding any insoluble residue) |
Table: Typical chemical ad physical properties of white Portland cement as per Indian Standards
Characteristics | IS: 8042-1989 |
1.     Chemical | |
a.      Insoluble residue % | Max. 2.0 |
b.     Iron Oxide % | Max. 1.0 |
c.      Magnesium Oxide % | Max. 6.0 |
d.     Sulphur Trioxide % | Max. 3.0 |
e.      Alumina/Iron Oxide % | Min. 0.66 |
f.       Lime Saturation Factor | 0.66-1.09 |
g.     Loss on Ignition % | |
2.     Physical | |
a.      Degree of wetness | |
i.              ISI scale | Min 70 |
b.     Fitness, Blaine M2/Kg (Specific surface) | Min 225 |
c.      Setting Time | |
i.              Initial | Min 30 |
ii.             Final | Max 600 |
d.     Compressive strength (Cement and Std. Sand Mortar 1:3) | |
i.               3 days (MPa) | Min 14.4 |
ii.             7 days (MPa) | Min 19.8 |
iii.           28 days (MPa) | Min 29.7 |
e.      Soundness | |
i.              Lechatliers method (mm) | Max 10 |
ii.             Autoclave expansion % | Max 0.8 |
How to remove white cement from tiles?
Cement is a necessary component of every building, and we can’t ignore it. The most troublesome aspect of the cement is that if it settles above the tiles, it might be hard to remove. The entire cement removal procedure is straightforward but time-consuming.
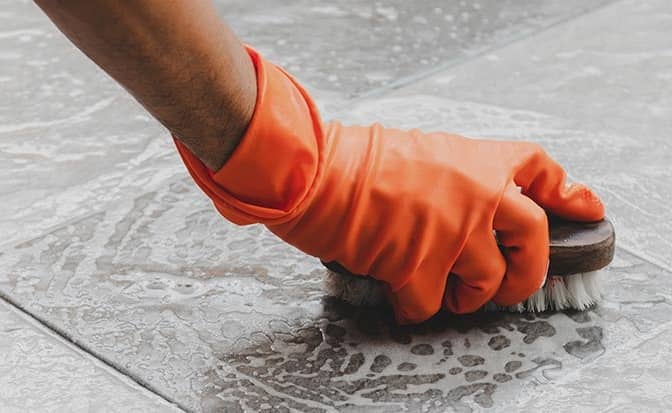
removing white cement from tiles
You must be steady and persistent in your efforts. If there is only a thin coating or a tiny amount of cement on the tiles, it may be removed using common home items. However, if there are numerous and deep layers of cement stains, you may need to use stronger acids. Let’s see how to get white cement off tiles.
Caution:Â
- To protect your skin and eyes, you should wear gloves, a coat, and glasses.
- Before you begin cleaning, make sure you have adequate ventilation.
- When the tile is glazed, take extra caution because even a moderate acid like vinegar might ruin the finish.
Things You Will Need:
- Gloves and goggles for protection
- Brush with a little brush or an old toothbrush
- Sponges or soft towels can be used.
- water in a bucket
- Detergent or soap
- vinegar (white)
- screwdriver with a flathead
- Scrubbing pad or Tampico brush
- Scrappers and phosphoric acid cleaner (optional for thick layers)
Also Read: Different varieties of cement
Different methods for removing Thin and Thick amounts of white cement
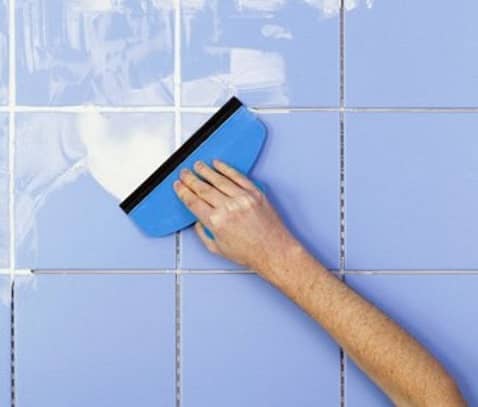
Removing Thin Layers of White Cement
Removing Thin Layers of White Cement (Method 1)
- Locate the areas where the cement stains may be seen and use white vinegar to remove tiny spots and thin layers. White vinegar has enough acidity to dissolve the cement between the tiles.
- Pour enough vinegar onto the cement and cover it with a sponge or soft cloth. Add extra white vinegar to the sponge and set it aside for an hour or two to allow the vinegar to solidify on the cement.
- Keep an eye on the vinegar’s dampness. If you believe it is evaporating owing to hot weather or other factors, reapply it as needed to maintain the area wet.
- It’s time to start cleaning them off once you see the cement is starting to loosen its grip on the tiles. Scrub the area with either a Tampico brush or a cleaning pad.
- Patience is key, as is being cool while cleaning for several minutes. Because the white vinegar has already loosened the cement, you’ll be able to see the scrubbed-out cement on the pad very quickly.
- After you’ve finished cleaning the area, wipe it down with a moist cloth. If there are still a few cement particles on the tiles, reapply vinegar and keep it on the tiles for a while. Check the results by repeating the procedure.
- After you’ve completed the operation, rinse the area with water. If you can’t use any more water in that region, fill a bucket with water and place a moist towel in it. Wipe the area and white cement particles with a damp towel.
- Finally, use soap and water to clean the afflicted area. Once the cement stains have been removed, it is critical to clean the white vinegar. Rinse the area twice more to ensure that the acid has been completely removed from the tiles.
Remove Large Amounts and Thick Layers of Cement (Method 2)
- To remove a bigger amount of white cement from tiles, use a powerful acid like Phosphoric Acid Cleaner. Acids of this type can eat through cement layers. Because the cement will gradually lose touch with the tiles, you may readily remove it.
- Remove the thick layers with a scraper or metal scrubber before administering the acid. A flat-head screwdriver can also be used. All these items, including the phosphoric acid cleanser, may be found in a hardware shop. You may also order them from the comfort of your own home.
- For the remaining white cement, it’s time to employ the powerful acid. Apply the acid according to the manufacturer’s directions. Remember To Wear Your Gloves, Coat, And Protection Glasses When Using The Phosphoric Acid Cleaner.
- The cement has already begun to lose touch with the tiles, as you can see. Scrub the area with a scrubber after half an hour or an hour to remove the white cement from the surface.
- Finally, thoroughly cleanse the area with clean water. To eliminate any leftover acid or acidic odor, thoroughly clean the surface and affected areas with soap and water. Thoroughly rinse the soap or detergent.
How to remove cement stains from tiles is a simple task. When working with acids, though, you must take extra care. Also, always adhere to the directions. Always mix the acid with water if the instructions say to. It can make the acid milder by diluting it, but it’s not always the greatest mix for your essential tiles.
How to use white cement on the wall?
- Prepare the surface
- Prepare the mixture (2:1)
- Whitewash the walls
How to mix white cement with water?
The conventional white cement mix calls for mixing the white cement with water in a 2:1 proportion of water to white cement. It’s also important to remember that water and white cement must be combined thoroughly without creating lumps and have the consistency of paint.
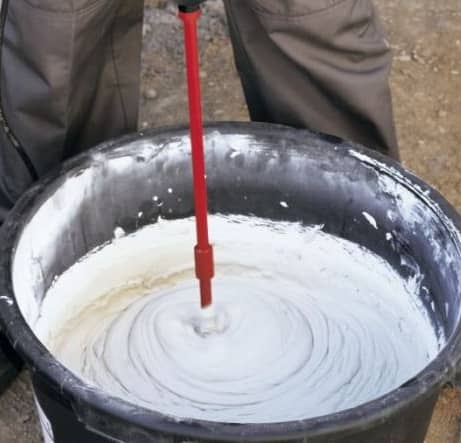
mixing white cement with water
How white cement is manufactured?
Since the white cement production process is identical to that of Portland cement, we’ll go through the elements that influence cement quality. The white cement production process, like that of a normal cement factory, maybe broken down into six steps:
- Primary crushing is used in most carbonate compositions. Because fine particles contain a high concentration of dye oxides, it is best to filter the fine particles before putting them into the cement crusher. Individually, the clay components are generally shattered.
- Cement raw materials grinding: the cement mill should grind the majority of the cement raw materials, and the grinding body cannot include iron. In terms of fineness, the white cement production method necessitates a smaller particle size than Portland cement.
- Homogenization: Only at microscopic scales can homogenize raw materials be said to be heterogeneous. The white cement manufacturing process requires a lot of homogenizations since the multi-component combinations are more prone to segregation than the raw materials used in grey cement production lines.
- Clinker production: There is a variety of preheating and calcining systems available, and which is best depends on whether the current plant has to be renovated and how much the plant operators are willing to invest in the project. The suggested group includes the cement rotary kiln and cyclone preheater.
- Grinding: Cement is manufactured from cement clinker and thickening additives such as gypsum or anhydrite to manage the thickening time. Gypsum is typically crushed with a jaw crusher; 90% of the particles are less than 6mm in size, with the largest size being 80mm.
- Packing and shipping: completed cement is usually stored in a cement silo, and white cement can be packed or shipped in bulk depending on the use.
Composition of white cement?
The manufacturing process of white cement is the same as that of grey cement, but the selection of raw material is an important part of the manufacturing process. Chrome, manganese, iron, copper, vanadium, nickel, and titanium oxides give the cement a grey hue. These basic ingredients are used in the smallest amounts possible in the production of white cement.
Limestone and clay are used as prominent raw materials for the manufacture of white cement. The manufacturing process is the same as that of OPC cement, the only differences are the heat required for the burning of raw material is more and fineness is more.
Also Read: Composition of Cement Clinker
White Cement VS Portland Cement/Grey cement
Similarity:
- Two are silicate cements, which use calcareous and Salic minerals as raw materials. These materials are calcined into cement clinker in a cement rotary kiln, then gypsum and admixture are added, and the clinker is crushed into white cement or Portland cement.
- Hydration products, such as hydrated silicate gel CSH, Ca (OH)2, ettringite Aft, and others, are essentially the same.
- Strength, setting, rheological property, durability, and other physical and mechanical properties. Use for both decorative and structural cement.
Difference:
- High demands on the white cement production process: producing high-quality white cement is tough since it necessitates high-quality raw ingredients, a precise grinding process, and calcination. The calcination temperature of white cement can reach 100-150°C.
- Cement clinker material composition: white cement clinker includes 10-15% tricalcium silicate, 15-20% silicate minerals, no iron phase minerals, and free calcium oxide, which is commonly used for Portland cement.
- White cement typically contains limestone and dolomite, whereas Portland cement contains fly ash, slag, and volcanic ash as admixtures.
- White cement has a finer texture than Portland cement.
- Part of the property: the heat of hydration, fluidity, setting time, shrinkage, and brittleness have various variation trends.
Raw materials used to make white cement
- Limestone -High Carbonate & Low Iron.
- Clay – High Alumina and Low Iron
- Oil / Pet Coke / Rubber
- Gypsum / Selenite
Table: Comparison between Grey and white cement
Properties | Grey Cement | White Cement |
Raw Materials | Iron Oxide and Manganese Oxide are abundant in raw materials. | Iron Oxide and Manganese Oxide are in extremely small quantities in raw materials comparatively. |
Fineness | It’s usually coarser than white cement. | Gray cement is usually finer. |
Kiln Fuel | Coal, petroleum coke, fuel oil, natural gas. | To avoid coal ash pollution, oil is applied. |
Energy Consumption | Low. | High. |
Cost | It is less costly. | Costlier than grey cement. |
Properties of White Cement
- Whiteness: Whiteness is a basic color criterion; on the domestic market, white cement must be between 80 and 84 percent white; on the foreign market, white cement must be between 84 and 88 percent white.
- Fineness: the finer the cement, the more surface area it has, the faster it hydrates, and the more durable it is. Cement quality is determined by its fineness.
- Strength: Another common benchmark, cement strength is affected by a variety of parameters such as clinker constituent minerals, sintering degree, crystalline condition, cement fineness, admixture activity, cement particle gradation, and so on.
- Setting time: White Portland cement must have an initial setting time of more than 45 minutes and a final setting time of fewer than 10 hours, according to Chinese national standards.
Also Read: Properties of high alumina cement
Table: Properties of white cement and their values
Properties | Value |
Fineness | 395 m2/kg |
Setting Time | 100 min |
Compressive Strength | |
1 day | 21 MPa |
2 days | 38 MPa |
7 days | 61 MPa |
28 days | 74 MPa |
Compact Density | 3150 kg/m3 |
Bulk Density | 1100 kg/m3 |
Brightness | 87% |
How to use white cement for painting?
Because white cement has more characteristics than grey cement, it is often used before painting. It’s ideal for coating the walls before you start painting. For the house’s bricklaying operations, grey cement is preferred. Many people also choose white cement for exteriors since it has a nicer polish than other types of cement. The application of white cement is a simple process. The technique of applying white cement is also known as ” Wash ” or ” Whitewash.” Unlike grey cement, white cement simply requires water.
The conventional white cement mix calls for mixing the white cement with water in a 2:1 proportion of water to white cement. In most cases, two coats of this mixture are required to evenly cover the walls. It’s important to remember that the walls should be thoroughly cleaned, and the surface levelled before applying the white cement to provide a decent finish. It’s also important to remember that water and white cement must be combined thoroughly without creating lumps and have the consistency of paint.
Consider the following factors while applying white cement:
- To begin with, you should be aware that whitewash should only be used on freshly plastered walls or walls that are free of lime, oil paints, and other contaminants.
- Paint your walls with lime or oil paint to brighten them up. Before you apply the white cement, make sure you scrape it completely.
- Making the mixture is the next crucial stage. It’s never a good idea to add water to cement instead of the other way around.
- After you’ve added the water, stir it with a mechanical stirrer to make sure there are no lumps.
- Whitewashing should only be done in well-ventilated locations.
The benefits of using white cement before painting
- Because white cement contains iron and magnesium, it gives the walls with adhesive strength.
- In contrast to grey cement, it also can withstand stains.
- Whitewashing the walls provides the color a great gloss.
- It also aids in priming the walls in preparation for painting.
- If you apply the white cement before painting, you won’t require a priming coat.
- It also serves as a foundation for the color of the paint.
- Unlike ordinary Portland grey cement, it makes the colors shine out since it is white.
- It’s completely safe to use
- In addition, when the cement absorbs it, the amount of paint required decreases, and absorption is low.
- It’s safe to use on any sort of paint.
Finally, putting white cement to walls before painting can help you get a beautiful finish since the color will show up more on whitewashed walls. Whitewashing is more durable than lime wash and lasts longer. It also fills in the cracks and prepares the walls for painting.
Uses of white cement
- White Portland cement has physical qualities that are comparable to conventional Portland cement. It is mostly used as a decorative material for structures, but it is also utilized in art.
- Putty powder, coating, caulking agent, binder, waterproof coating, terrazzo, fake stone, floor tile, permeable brick, washing stone, sculpture, wear-resistant floor, color cement, and so on are all examples of white cement applications.
Measures To Improve Whiteness of White Cement
- Improve the whiteness of the clinker. A moderate reduction atmosphere should be used for calcination. The fuel is natural gas, gas, or liquid fuel with no ash powder.
- Improve the whiteness of the gypsum. Add some higher-whiteness gypsum to the cement grinding mill to increase the fineness of the cement.
- Prevent sundries from being mingled. During calcination, grinding, transportation, and packaging, reduce sundries such as grinding mill lining material.
Different suppliers market rates of white cement
Supplier | Market rate | Remarks |
Jhonson chemicals private Ltd. | 580 Rs per Kg | Decorative cement |
Ashapura minichem Ltd. | 890 Rs per bag | Advance Decorative cement |
Vedant chemicals enterprise | 23 Rs per Kg | Decorative cement |
Peekay agencies private Ltd. | 800 Rs per bag |
White cement HSN code?
White cement HSN code is 252321.
Also Read: 6 Things to Consider Before Hiring Commercial Painters
Leave a comment